Автор: Alan Records Ken Sutherland | Elsevier Science.
Тип документа: Справочник | pdf.
Популярность: 0.09 %
Страниц: 439.
Размер файла: 16 Mb.
Язык: Английский.
Год издания: 2001.
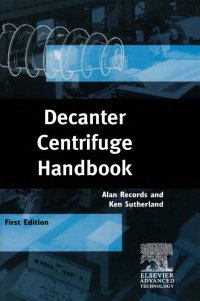
The decanter centrifuge has become a major processing tool in a wide range of liquid/solid separation applications. This handbook aims to be a thorough introduction to the design, performance and application of the decanter. It aims also to be a useful guide for the centrifuge engineer, both in equipment manufacturing companies and in the end-user companies, and their associated contractors and consultancies.
The handbook's first chapter introduces the reader to the decanter, to its history and to the manufacturing sector within which it is made. The contents of this chapter are intentionally brief, with major expansion of the topics covered in later chapters of the book.
CONTENTS
Preface and Acknowledgements
Chapter 1 Introduction
1.1 The Decanter Centrifuge
1.1.1 The basic decanter
1.1.2 Separation principle
1.1.3 Decanter applications
1.2 The History of the Decanter
1.2.1 Origins
1.2.2 Machine and application development
1.3 Decanter Manufacturers
1.4 Present Trends
1.5 References
Chapter 2 Decanter Design
2.1 Basic Construction
2.2 Basic Components
2.2.1 Orientation
2.2.2 Flow
2.2.3 Materials of construction
2.2.4 Bowl
2.2.4.1 Front hub
2.2.4.2 Centrate weirs
2.2.4.3 Liner
2.2.4.4 Front hub bearing
2.2.5 Beach
2.2.5.1 Rear hub and bearings
2.2.5.2 Cake discharge
2.2.5.3 Liner
2.2.6 Conveyor
2.2.6.1 Conveyorhub
2.2.6.2 Flights
2.2.6.3 Feedzone
2.2.6.4 Floe/rinse zone
2.2.6.5 Wear protection
2.2.6.6 Conveyor bearings and seals
2.2.7 Gearbox
2.2.8 Frame
2.2.8.1 Bearing supports
2.2.8.2 Feed tube
2.2.8.3 Vibration isolators
2.2.9 Casing
2.2.9.1 Casing baffles
2.2.9.2 Cake discharge
2.2.9.3 Centrate discharge
2.2.9.4 Casing seals
2.2.9.5 Vents
2.2.10 Sub-frame
2.2.11 Maindrive
2.2.12 Back-dri ve Variations to Main Components
2.3.1 Orientation
2.3.1.1 Vertical vs. horizontal
2.3.1.2 Vertical decanter seals and bearings
2.3.1.3 Vertical decanter casing seal
2.3.2 Flow
2.3.3 Materials of construction
2.3.4 Bowl variants
2.3.4.1 Front hub
2.3.4.2 Centrate weirs
2.3.4.3 Liner
2.3.4.4 Mainbearing
2.3.5 Beach
2.3.5.1 Rearhub
2.3.5.2 Cake discharge
2.3.5.3 Beach liner
2.3.6 Conveyor
2.3.6.1 Conveyor hub
2.3.6.2 Flights
2.3.6.3 Feedzone
2.3.6.4 Floc/rinsezone
2.3.6.5 Wear protection
2.3.6.6 Bearings and seals
2.3.7 Gearbox
2.3.8 Frame
2.3.8.1 Bearing supports
2.3.8.2 Feedtube
2.3.8.3 Vibration isolators
2.3.9 Casing
2.3.9.1 Baffles
2.3.9.2 Cake discharge
2.3.9.3 Centrate discharge
2.3.9.4 Casing seals
2.3.9.5 Vents
2.3.10 Sub-frame
2.3.11 Main drive
2.3.12 Back-drive
Special Features
2.4.1 Basic construction
2.4.1.1 Screen-bowl decanter
2.4.1.2 Three-phase decanter
2.4.1.3 The countercurrent extractor decanter
2.4.1.4 Decanters for temperature and pressure extremes
2.4.1.5 The cantilevered bowl
2.4.1.6 The “hubless” conveyor
2.4.1.7 Thickening decanter
2.4.1.8 The dual beach decanter
2.4.2 Centripetal pump
2.4.3 Skimmer pipe
2.4.4 Centrate weir design
2.4.4.1 Cup dam
2.4.4.2 Notched dam
2.4.4.3 Inflatable dam
2.4.5 Noise suppression
2.4.6 Bowl baffles
2.4.6.1 Cake baffle disc
2.4.6.2 Baffle cone
2.4.6.3 Floater disc
2.4.6.4 Conveying baffle
2.4.6.5 Longitudinal baffle
2.4.7 Clarification enhancement
2.4.7.1 Ouasi-axial flow
2.4.7.2 Fully axial flow
2.4.7.3 Vanes
2A.7A Discs
2.4.8 Conveyor rake
2.4.9 Conveyor tiles
2.4.10 Conveyor pitch
2.4.10.1 Variable pitch
2.4.10.2 Reversepitch
2.4.11 Counterbalance and scraper flights
2.4.12 Feedzone
2.4.13 The reslurry collector
2.4.14 CIP
2.4.15 TheRotodiff
2.4.16 Power regeneration
2.4.17 Dual main drive motor
2.4.18 Floating conveyor
2.4.19 Decanter controls
2.5 References
Chapter 3 Applications
3.1 Application Classes
3.2 Application Analysis
3.3 Waste Sludge Processing
3.3.1 Industrial wastes
3.3.2 Water treatment sludges
3.3.3 Municipal sewage treatment
3.4 Energy Materials Production
3.5 Processed Fuels
3.6 Minerals Extraction and Processing
3.7 Food and Food By-Products
3.7.1 Meat and meat products processing
3.7.2 Fish processing
3.7.3 Fruit and vegetable products
3.7.4 Other food processing
3.8 Beverages
3.9 The Chemicals Industry
3.9.1 Bulk inorganic chemicals
3.9.2 Bulk organic chemicals
3.9.3 Fine and household chemicals
3.9.4 Pharmaceutical and medicinal chemicals
3.10 Other Applications
Chapter 4 Decanter Theory
4.1 Basic Theories
4.1.1 Acceleration force
4.1.2 Differential
4.1.3 Conveyor torque
4.1.4 Process performance calculations
4.2 Particle Size Distribution
4.3 Clarification
4.3.1 Sigma theory 4.3.1.1 Usingsigma
4.3.2 Sigma enhancement
4.3.3 Flocculant requirement
4.4 Classification
4.5 Three-Phase Separation
4.6 Thickening
4.7 Conveying
4.7.1 The Beta theory
4.7.2 Conveying on the beach
4.7.3 Dry solids conveying
4.8 Conveyor Torque
4.9 Dewatering and Washing
4.9.1 Solids dewatering
4.9.2 Washing
4.9.3 Solids compaction
4.10 Dry Solids Operation
4.11 FluidDynamics
4.11.1 Reynolds number
4.11.2 Moving layer
4.11.3 Cresting
4.11.4 Feed zone acceleration
4.12 Power Consumption
4.12.1 Main motor sizing
4.12.2 Main motor acceleration
4.13 Mechanical Design
4.13.1 Maximum bowl speed
4.13.2 Critical speeds
4.13.3 Liquid instability problems
4.13.4 Length/diameter ratio
4.13.5 Bearing life
4.13.6 Gearbox life
4.13.7 Feed tube
4.14 Nomenclature
4.15 References
Chapter 5 Flocculation
5.1 The Principle of Flocculation
5.2 Polymer Solution Make-Up
5.2.1 Dissolving solid polymers
5.2.2 Diluting dispersions
5.2.3 Final flocculant solution characteristics
5.3 Polymer Choice
5.4 Pretreatment
5.5 Admitting Flocculant to the Decanter
5.6 Flocculant Suppliers
5.7 Low-Toxicity Polymers
5.8 Applications
5.9 Performance
5.10 References
Chapter 6 Test Work and Data
6.1 Test Equipment
6.2 Test Procedures
6.3 Test Log
6.4 Some Test Data
6.4.1 Spent grain
6.4.2 Agricultural products
6.4.3 Lime sludge classification
6.4.4 Clay classification
6.4.5 Waste activated sludge thickening
6.4.6 Digested sludge thickening
6.4.7 Lactose washing
6.4.8 Coal tailings dewatering
6.4.9 Dry solids (DS) dewatering
Chapter 7 Calculations and Scaling
7.1 Basic Calculations
7.2 Three-Phase Calculations
7.3 Classification Calculations
7.4 Washing
7.5 The Probability Scale
7.6 Scale-Up of Centrate Clarity Limiting Applications
7.7 Simple Dewatering and Torque Scale-Up
7.8 Main Motor Sizing
7.9 DS Scaling
Instrumentation and Control
8.1 Decanter Plant Modules
8.2 Instrumentation
8.2.1 Flowmeters
8.2.2 Solids concentration meters
8.2.3 Level probes
8.2.4 Speed probes
8.2.5 Temperature probes
8.2.6 Torque measurement
8.2.7 Timers
8.2.8 Counters
8.2.9 Electrical meters
8.2.10 Bearing monitors
8.3 Controlled Equipment
8.3.1 On/off devices
8.3.2 Variable output devices
8.4 Controllers
8.5 Integrated Controller
8.6 CIP
8.7 References
Chapter 9 The Decanter Market
9.1 Market Characteristics
9.2 Market Trends 5
9.3 Market Size Estimates
9.3.1 Overall decanter market size
9.3.2 Regional market estimates
9.3.3 Application market estimates
9.3.4 Suppliers’market shares
Chapter 10 Suppliers' Data
Chapter 11 Glossary of Terms
Preface and Acknowledgements
By virtue of its title, which involves the word “handbook”, this book is intended, above all else, to be useful. Its aims include the explanation of the nature and methods of operation of the decanter centrifuge, and a description of the kind of performance that might be expected from a decanter.
The decanter centrifuge is a device for continuously separating particulate solids from a suspending liquid or liquids by sedimentation and decanting. As such, it is part of the general range of sedimenting, filtering and other mechanical equipment used for separation processes. A distinguished range of books exists that describes this complete spectrum of equipment, and the processes by which they operate. A previous book covers the whole range of centrifuges, both sedimenting (like the decanter) and filtering, but this is the first book to deal solely with the solid-bowl, scroll-discharge centrifuge, which is the decanter.
The book is aimed at all those for whom the decanter may be part of their studies, of their research, or of their working life. It is intended to be of value in undergraduate courses on filtration and separation, but it will also offer the practising engineer in end-user companies much that is of direct value to the daily job of designing, specifying or operating this sophisticatedly engineered, but very useful, piece of processing equipment. This handbook will find use in research establishments and equipment manufacturers’ engineering departments, as it gives guidance on basic design and operating features, some in regular use and some only recently introduced to the market.
This essentially practical text nevertheless covers the underlying theory of centrifugal sedimentation separations in some detail, which further extends its usefulness to the research or design engineer looking for new ideas.
The arrangement of the handbook follows a logical pattern: a general introduction, followed by technical descriptions of equipment features and the industrial uses of the decanter. Then comes the theory of the decanter's design, and detailed descriptions of operational and test procedures. The book finishes with some marketing data, and descriptions of the equipment ranges of the main manufacturers.
The authors (both Chartered Chemical Engineers) have a wealth of experience in the decanter business:
Alan Records retired from a senior equipment application and development role with Alfa Laval, after almost a full lifetime's job involved with decanters, covering research, design, commissioning, operation and service, in a wide range of industrial applications; and Ken Sutherland, for a time Technical Manager for Sharpies, has later been heavily involved with the marketing aspects of separation equipment, including centrifuges.
The putting together of a book of this nature requires the help and co¬operation of many individuals and organisations. The contributions, help, advice, work and kind permissions of those mentioned below are most gratefully acknowledged.
Lenny Shapiro and Jan Cederqvist contributed to the mechanical information, while Bert Guille assisted with the electrical content. The process data were obtained as a result of painstaking work in the field, often in far less than a salubrious environment, by numerous field engineers, our former colleagues, and in particular John Joyce, Betina Pedersen, and Keith Smith. Apologies are extended to all those not mentioned.
Denis Locke contributed to the work on many of the illustrations, professionally executed by Mike Nicklinson.
Graham Dawson, with the help of some of his former colleagues, advised on the section on flocculant technology. Keith Kernahan advised on the details of the Viscotherm equipment.
The Triton Electronic Company co-operated in providing photographs and details of their CST equipment.
The decanter centrifuge market is a highly competitive one, and thus manufacturers are, understandably, reticent in providing specific data and information on their products. Without such data and information, however, this book would be reduced in value. The authors are therefore especially grateful for the data supplied by the companies Alfa Laval. Baker Process (Bird Machine and Bird Humboldt), Broadbent. Centriquip. Centrisys, Flottweg. Gennaretti, Guinard, Hiller, Hutchison-Hayes, Noxon, Pennwalt India, Pieralisi, Siebtechnik, and Westfalia/Niro. Permission to reproduce sketches and drawings has been obtained from Alfa Laval, Bird Machine, Bird Humboldt, Broadbent, Centriquip, Centrisys. Cyclo, Flottweg, Noxon, Siebtechnik, Tomal, Viscotherm and Westfalia Separator.
Finally, gratitude is expressed to Bent Madsen and his colleagues for checking the early manuscripts. The book owes its origin to Nick Corner- Walker, then Director of Engineering with Alfa Laval, to whom the authors are indebted for the inspiration, for his personal support, and for putting the resources of a major manufacturer of decanters behind the venture. The authors are very happy to acknowledge that debt here, but also to acknowledge the input from the other companies whose ideas and illustrations have been used at the appropriate parts of the text.
To these, and all of the other workers involved with the decanter for the years of its effective operating history, the authors express their thanks.
Скачать бесплатно: Decanter Centrifuge Handbook 1-st Edition.